
Veränderungen und Verbesserungen mit zufriedenen Mitarbeitern und Buchhaltern*
* Vorausgesetzt, Ihre Buchhalter verstehen auch die wahre Kraft von True Lean.
Wie eine gesunde und effektive Organisation aussieht.
Als der inzwischen pensionierte Isao Yoshino 1966 als Management-Trainee bei Toyota anfing, bestand eine seiner ersten Aufgaben darin, Autolacke aus Komponenten zusammenzusetzen und zu mischen.
Er erhielt von seinem Vorgesetzten Anweisungen* zum Mischen der Farbkomponenten. Nach seiner Ausbildung wurde er seiner Arbeit allein überlassen.
Einige Zeit später gab es Beschwerden, dass der Autolack nicht trocknete. Sein Vorgesetzter ging zu Isao und statt ihm Vorwürfe zu machen, begegnete ihm sein Vorgesetzter mit Respekt und Wertschätzung. Er gab an, dass sein eigener Unterricht wahrscheinlich unzureichend sei.
In einer normalen Organisation würde der Manager dem Mitarbeiter sagen, er solle nie wieder die falsche Dose verwenden! Dies würde im Tagesbericht als „Mit dem Mitarbeiter besprochen und Problem gelöst“ erscheinen.
Nicht bei Toyota! Was folgte, war ein Beweis für die respektvolle Führung von Toyota, gepaart mit kontinuierlicher Verbesserung. Gemeinsam untersuchten sie die Ursachen und fanden eine einfache und wirksame Lösung. Anschließend testeten sie die Lösung und aktualisierten die Anweisungen mit der Begründung, warum sie die Änderung vorgenommen hatten**.
Diese Anekdote unterstreicht die Kraft einer psychologisch sicheren Umgebung, in der den Mitarbeitern nicht die Schuld für Fehler gegeben wird – der Eckpfeiler der Führungsprinzipien von Toyota. Durch Respekt vor den Menschen, kontinuierliche Verbesserung und akribische Liebe zum Detail schafft Toyota ein großartiges Arbeitsumfeld, in dem das Lernen und der Aufbau individueller Fähigkeiten sowie die Pflege einer Kultur der kollektiven Unterstützung im Mittelpunkt stehen.
Das hört sich so einfach an, aber es funktioniert nur, wenn man weiß, wie man die richtige Unternehmenskultur schafft
und Sie allgemein anerkannte Geschäftspraktiken und Richtlinien, die dies verhindern, Vermeiden.
*Danke an Katie Anderson, die Isao Yoshino interviewt hat.
Bild von ipic.ai
* TWI = Training within Industry. On-the-Job-Training basierend auf drei Prinzipien: Arbeitsbeziehungen (frei von Schuldzuweisungen, psychologisch sicher), Job-Methoden (kontinuierliche Verbesserung), Job-Anweisungen (On-the-Job-Training basierend auf aktuellen Best Practices/Arbeitsanweisungen)
** Dies wird oft übersprungen, da der Grund zu diesem Zeitpunkt offensichtlich erscheint, aber ohne eine Beschreibung, warum dies getan wurde, kann man später nicht heruasfinden, ob ein alter Prozessschritt noch erforderlich ist.
*** Reputation, Supportanrufe, Produktrückrufe usw. Die meisten Unternehmen denken, dass hohe Qualität teuer ist, weil sie nicht wissen, was zur Herstellung qualitativ hochwertiger Produkte erforderlich ist, und versuchen, dies durch Qualitätsprüfungen zu erreichen. True Lean zeigt uns, dass hohe Qualität günstiger ist und zu zufriedeneren Mitarbeitern führt.
Glück ist nicht die Abwesenheit von Problemen,
sondern die Fähigkeit, mit ihnen umzugehen
Erfahren Sie, wie Sie Ihre True-Lean-Transformation effektiv führen
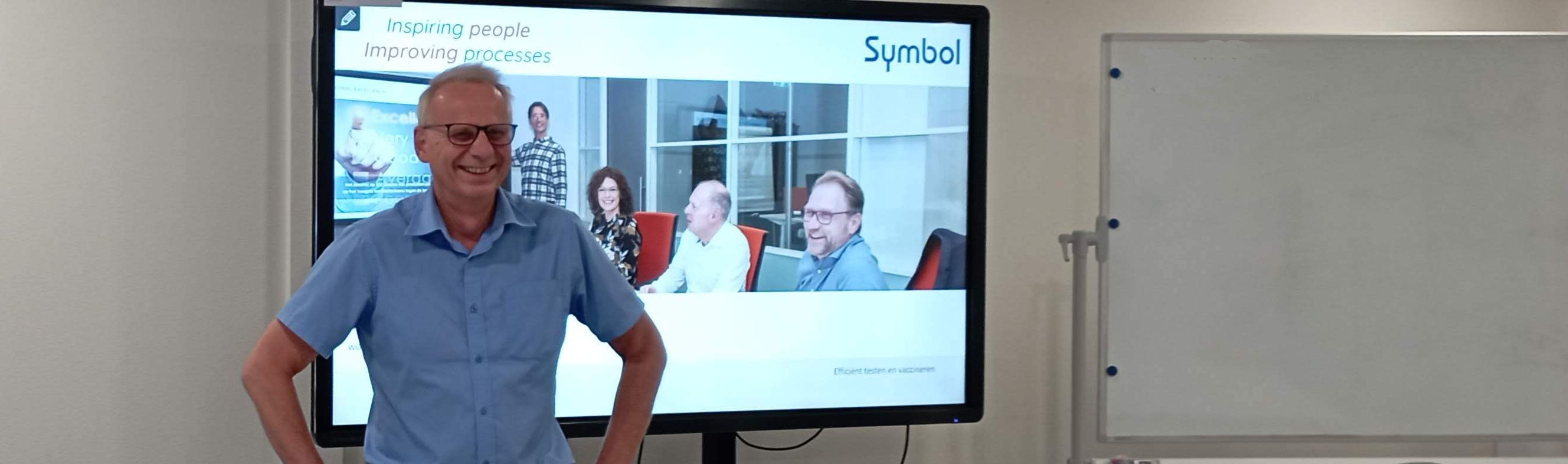
Entdecken Sie die Kraft von True Lean-Führung
Eine echte Lean-Transformation ist wahrscheinlich eine der bedeutendsten Veränderungen, die in Ihrem Unternehmen stattfinden werden. Als Führungskraft spielen Sie daher eine entscheidende Rolle bei der Steuerung dieser Transformation. Es ist von entscheidender Bedeutung, die True-Lean-Prinzipien, ihre Auswirkungen und Herausforderungen für Sie und Ihr Team zu verstehen. Dies ist ein Prozess, der nicht delegiert oder ausgelagert werden kann. Man muss von vornherein führen, natürlich mit guter Unterstützung durch externe Expertise.
Nehmen Sie an unserem mehrtägigen interaktiven „True Lean Workshop für Organisationsleiter“ teil.* Dieser Workshop wird auf die individuellen Bedürfnisse Ihrer Organisation zugeschnitten und bietet einen großartigen Überblick über die Grundlagen von True Lean mit praktischen Übungen und praktischer Erfahrungen. Sie haben die Möglichkeit Ihr neues Wissen direkt am Arbeitsplatz anzuwenden.
Basierend auf mehr als 30 Jahren Erfahrung in verschiedenen Organisationsrollen (vom Mitarbeiter bis zum GF) und in unterschiedlichen Unternehmenstypen beleuchtet unser Workshop die entscheidende Rolle der Führung beim Übergang zu True Lean. Sie lernen die Schritte zu einer Kultur der kontinuierlichen Verbesserung, des Vertrauens und der Selbstbestimmung kennen.
Entscheidend ist, dass wir verstehen, warum „Lean“-Initiativen nach einem kurzen anfänglichen Erfolg oft zu mittelmäßigen Ergebnissen oder sogar zu Chaos führen. Indem Sie die zugrunde liegenden Prinzipien entschlüsseln und gängige Missverständnisse entlarven, gewinnen Sie Klarheit darüber, was tatsächlich passiert und wie Sie diese Rückschläge umkehren können.
Aber das ist nicht alles. Wir beleuchten auch die subtilen, aber tiefgreifenden Fallstricke, die in traditionellen Organisationen lauern. Von veralteten, traditionellen Unternehmensrichtlinien bis hin zu schädlichen HR-Protokollen oder Buchhaltungsrichtlinien*** – diese unsichtbaren Barrieren können selbst die gutgemeintesten Lean-Initiativen zum Scheitern bringen. Indem Sie diese Hindernisse sofort erkennen und angehen, vermeiden Sie die Fallstricke, in denen viele Unternehmen stecken bleiben.
** True Lean bezieht sich auf den ganzheitlichen Ansatz, der auf den Prinzipien der kontinuierlichen Verbesserung und des Respekts gegenüber den Menschen basiert. Im Gegensatz zu den oberflächlichen, werkzeugbasierten Implementierungen, die in vielen Organisationen vorherrschen, legt True Lean Wert auf kulturelle Transformation und organisatorische Exzellenz.
*** Einige allgemein anerkannte Methoden wie die Kostenrechnung sind NICHT GAAP-konform, werden aber dennoch verwendet.
Die Mitarbeiter sind nicht das Problem, sie sind die Lösung
Essentrium, Rembrandtlaan 27, 6881CP Velp die Niederlande IHK Nr.: 59376023 USt-IdNr. NL001190095B55