
Van crisis naar succes
En dat al 75 jaar lang
Werken aan een gezonde planeet in een zorgzame, effectieve, stabiele en succesvolle organisatie.
Hallo, mijn naam is Robert Ilbrink, de oprichter van Essentrium (2005).
De missie van Essentrium is het bijdragen aan een betere planeet voor mens en dier.
Na een lange zoektocht en veel eigen ervaring over wat werkt én plezier geeft, ben ik zo’n 20 jaar geleden uitgekomen bij Dr. W. Edwards Deming.
Waarom Deming?
Omdat Deming een management filosofie heeft die bewezen* beter is dan het alom gebruikelijke Angelsaksische model.
* Toyota bewijst dit al 75 jaar, maar ook andere ondernemingen laten het keer op keer zien. Helaas wordt dit iedere keer weer ongedaan gemaakt door Angelsaksische (MBA) leiders die niet voor de lange termijn kiezen, maar voor de korte termijn. Zie verderop over de successen en terugval van Ford.
Beter? Hoezo beter?
Kijk naar zijn invloed op de Japanse industrie na de Tweede Wereld Oorlog. De Japanse industrie stond bekend om zijn slechte kwaliteit. Mede daarom verplichtten de geallieerden dat op alle Japanse export producten een vermelding stond “Made in Japan”.
Toen Deming in 1950 in Japan begon met het onderwijzen van zijn methode (aan ruim 80% van de CEO’s van de Japanse maakindustrie), transformeerde de industrie en werd deze zelfs een gevaar voor de westerse industrie omdat de Japanse industrie hoge kwaliteit producten leverden, met een lange levensduur, lage onderhoudskosten en tegen goed betaalbare prijzen. Deming liet ze zien hoe je dat doet met enthousiast samenwerkende medewerkers én leveranciers. De waarschuwing “Made in Japan” werd een kwaliteitszegel.
Toyota is één van de meest bekende Japanse bedrijven die deze filosofie volgt. Toch heeft Deming in zijn eigen vaderland een grote invloed gehad.
In 1980 heeft Ford in de VS de hulp van Deming ingeroepen. Ford stond eind jaren 70 op omvallen. Slechts een paar jaar later werden de nieuwe Ford modellen uitgeroepen tot de beste auto’s door het kritische blad “Consumer Reports”. De medewerkers waren opgetogen en gaven aan nooit meer terug te willen naar het oude Angelsaksische systeem. En Ford maakte nog nooit zoveel winst. Meer winst dan de concurrenten GM en Chrysler samen.
Totdat er een (Angelsaksische) CEO gekozen werd, die niets van de Deming filosofie begreep, en de winst verder wilde opdrijven door flink in de kosten te snijden….
Het ging nog even goed (vliegwiel effect), maar een paar jaar later zakte de kwaliteit weer, viel de winst weer terug naar het oude niveau, en waren de medewerkers weer net zo ongelukkig als voorheen.
Wat heeft dit met een gezonde planeet te maken?
Één van de pijlers van de Deming filosofie is het continu verbeteren. Hierdoor maak je producten die niet snel weggegooid hoeven te worden, en wordt er tijdens het productieproces bijna geen energie en grondstoffen verspilt.
Lezing over de filosofie die Toyota al 75 jaar toepast.
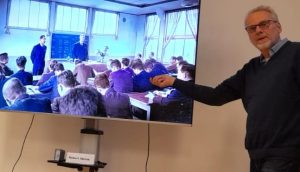
In een wereld waarin de natuur wordt uitgebuit en we kampen met een schijnbaar tekort aan gekwalificeerde en gemotiveerde medewerkers, is er dringend behoefte aan een duurzame en gezonde tegenhanger van de huidige zakelijke modellen.
Een methode die medewerkertekorten niet oplost door medewerkers harder of langer te laten werken, maar door het werk gemakkelijker, vlotter, interessanter, afwisselender en vooral voldoening gevend en stress-arm te maken.
Dr. Deming heeft Japanse (en later Amerikaanse) bedrijven geholpen om hoge kwaliteit tegen lage kosten (en met prachtige marges) te leveren. Zijn filosofie heeft in de Japanse industrie tot duurzame groei én financieel succes geleid, met tevreden en ontspannen medewerkers die fluitend naar hun werk gaan.
Van crisis naar kwaliteit, duurzaamheid en langdurig succes
Dr. Deming onderwees verbetermethodes en statistiek in de Amerikaanse oorlogsindustrie. In 1950 begon hij met lezingen over zijn managementprincipes voor de Japanse industrie, die destijds bekend stond om zijn slechte kwaliteit. Na 1960 zorgden de Japanse producten voor onrust in de VS. Japanse producten waren van hoge kwaliteit, gingen langer mee, hadden lagere onderhoudskosten en waren goed betaalbaar. En dat terwijl de kosten voor grondstoffen, energie en lonen in Japan hoger waren. Hoe deden ze dat? En hoe maakte Toyota zulke hoge marges dat ze intussen een reserve van $53 miljard konden opbouwen?In deze lezing worden twee bedrijven vergeleken in hun ontwikkeling.
Na een korte introductie van Dr. Deming en zijn filosofie, volgen we de ontwikkeling van twee bedrijven. Één bedrijf dat op de bekende Angel-Saxische manier geleid wordt, en één bedrijf dat volgens de Deming filosofie werkt. Al snel zien we dat de bedrijven en hun medewerkers een heel andere ontwikkeling doormaken. Hier worden de elkaar ondersteunende en versterkende aspecten van beide methodes in de praktijk zichtbaar. Zo leren we over de effecten van algemeen toegepaste managementmethoden en belichten we de zware crisis waarin Toyota terechtkwam toen ze de Deming regels een tijd lang negeerden. Aangekomen in het hier en nu, onderzoeken we de bijdrage die AI (Artificiële Intelligentie) in beide ondernemingen kan spelen.Aanbieding: Bedrijfsscan en een rapport met reflectiepunten en mogelijke verbeterpunten.
Een bedrijfsscan geeft inzicht in de effectiviteit en bedrijfscultuur.
Samen selecteren we waar de focus op komt te liggen. Voorbeelden van onderzoeksthema’s zijn:
- De samenhang tussen verkoop, inkoop, planning, productie/service, distributie en klantenservice doorlichten;
- Onderzoek naar de doelen en hoe die op de werkvloer uitgewerkt worden;
- In kaart brengen welke bedrijfscultuur er is en welke effecten die cultuur heeft op zaken als samenwerking en kwaliteit;
- Onderzoeken hoe de doorlooptijd en kwaliteit zijn, en wat de effecten daarvan zijn op de winstgevendheid;
- Onderzoeken hoe de medewerkers zelf over de organisatie denken.
Deze bedrijfsscan wordt u aangeboden voor slechts € 1’500,– all-in.
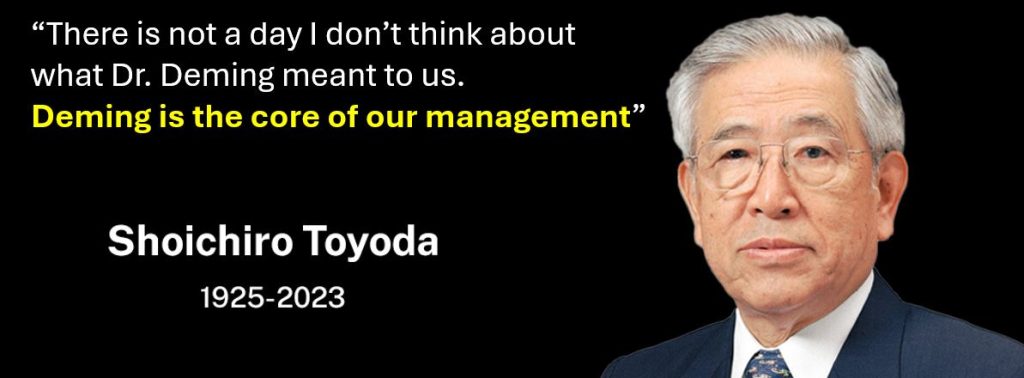
Hoe een gezonde en effectieve organisatie eruit ziet.
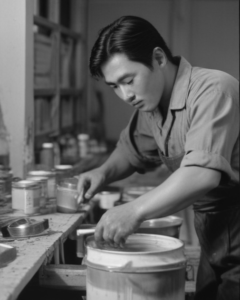
Van zijn leidinggevende kreeg hij instructies* over het mengen van de verfcomponenten. Na zijn training werd hij alleen gelaten om zijn werk uit te voeren.
Enige tijd later kwamen er klachten dat de autolak niet droogde. Zijn leidinggevende ging naar Isao, maar in plaats van hem de schuld te geven, benaderde zijn supervisor hem met respect en waardering. Hij gaf aan dat zijn eigen instructie waarschijnlijk niet toereikend was geweest.
In een normale organisatie zou de leidinggevende het nog een keer uitleggen en voordoen! Dit zou in het dagrapport komen te staan als “Besproken met de medewerker en probleem opgelost”.
Niet bij Toyota! Wat volgde was een bewijs van Toyota’s leiderschap van respect gecombineerd met continu verbeteren. Samen onderzochten ze de oorzaken en ontdekten ze een eenvoudige en effectieve oplossing om dit in de toekomst te voorkomen. Daarna testen ze de oplossing en pasten ze de werkinstructies aan, waarin ze ook beschreven waarom ze deze wijziging hadden doorgevoerd**.
Deze anekdote onderstreept de kracht van een psychologisch veilige omgeving waarbij medewerkers niet beschuldigd worden bij ontstane fouten, één van de hoekstenen van Deming’s (en Toyota’s) leiderschapsprincipes. Door respect voor mensen, voortdurende verbetering en nauwgezette aandacht voor details te omarmen, creëert Toyota een fijne werkomgeving waarbij leren en het opbouwen van individuele vaardigheden samen met het cultiveren van een cultuur van collectieve ondersteuning de kern vormen.
Dit klinkt zo simpel, maar het werkt alleen als je weet hoe je de juiste bedrijfscultuur kunt laten ontstaan en hoe je de
algemeen aanvaarde zakelijke praktijken en beleidsregels, die dit in de weg staan, kunt ombuigen.
Met dank aan Katie Anderson die Isao Yoshino interviewde
voor haar boek “Learning to Lead, Leading to Learn“.
Afbeelding door ipic.ai
* TWI = Training within Industry. On the Job training gebaseerd op 3 principes: Job Relations (Werk Relaties, psychologische veiligheid), Job Methods (Werk Methodes, continu verbeteren), Job Instructions (on the job training vanuit de actuele werkinstructions)
** Vaak wordt dit overgeslagen omdat de reden op dat moment voor de hand ligt, maar zonder beschrijving waarom dit is gedaan kun je later niet vaststellen of een oude processtap nog steeds nodig is.
Reputatieschade, meerwerk bij de helpdesk, terugroepen van producten, enz. Het niet weten wat er nodig is om producten van hoge kwaliteit te produceren, en dit dan maar proberen te bereiken door middel van kwaliteitsinspecties, is de reden waarom de meeste bedrijven denken dat hoge kwaliteit duur is. Dr. W. Edwards Deming en Toyota laten zien dat hoge kwaliteit goedkoper is én zorgt voor gelukkigere medewerkers.
Geluk is niet de afwezigheid van problemen,
maar het het vermogen om problemen aan te pakken
Leer de transformatie zelf effectief te leiden
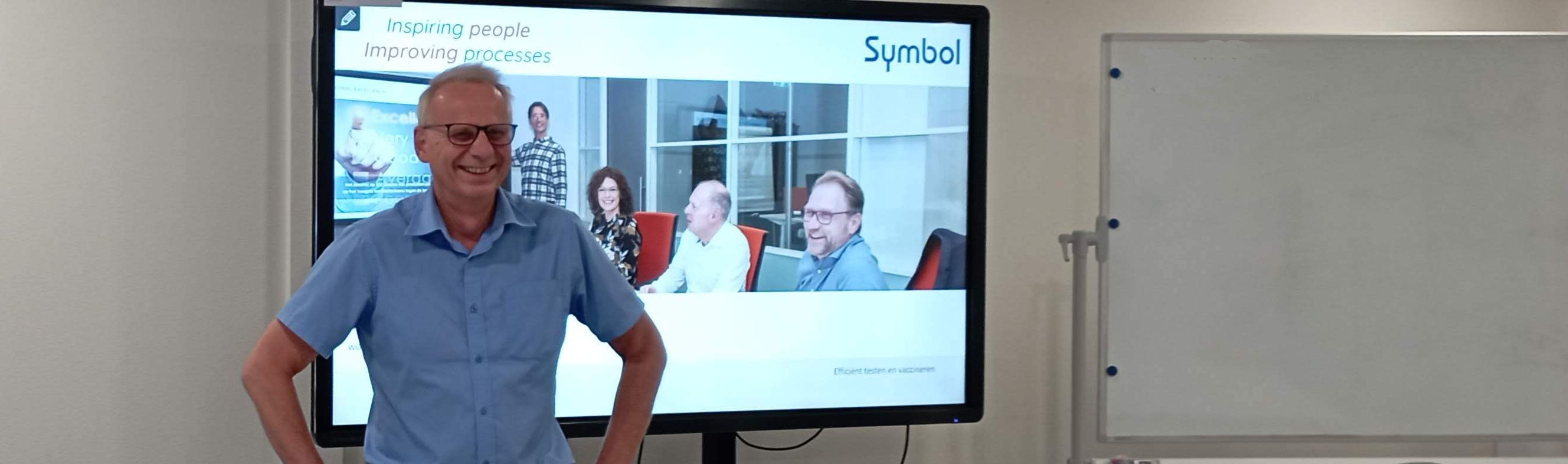
De kracht van Deming leiderschap ontsluiten
Een echte Deming transformatie is waarschijnlijk een van de meest ingrijpende veranderingen die in uw organisatie zal plaatsvinden. Als leider speel je daarom een cruciale rol in het sturen en begeleiden van deze transformatie. Het begrijpen van de succes-principes, de impact en uitdagingen voor zowel jouzelf als de teams is van cruciaal belang. Dit is een traject dat niet gedelegeerd of uitbesteed kan worden aan derden. Je moet leiding geven vanaf de voorkant, natuurlijk wel met goede ondersteuning door externe expertise.
Doe mee aan onze meerdaagse interactieve ‘Deming workshop voor leiders van organisaties.’* Deze workshop wordt afgestemd op de unieke behoeften van uw organisatie en biedt een goed overzicht van de fundamenten van True Lean met praktische oefeningen en praktijkervaring, waardoor u de mogelijkheid krijgt om uw nieuwe kennis direct op uw werkplek toe te passen.
Gebaseerd op meer dan 30 jaar ervaring in verschillende organisatierollen (van werknemer tot CEO) en in verschillende soorten bedrijven, belicht onze workshop de cruciale rol van leiderschap bij de transitie. U leert welke stappen nodig zijn voor het laten ontstaan van een cultuur van voortdurende verbetering, vertrouwen en echte samenwerking.
Cruciaal is het begrijpen waarom de meeste ‘Lean’-initiatieven, na een kort eerste succes, vaak matige resultaten of zelfs chaos opleveren. Door de onderliggende principes te ontrafelen en veelvoorkomende misvattingen te ontkrachten, krijg je duidelijkheid over wat er in werkelijkheid gebeurd en hoe u deze tegenslagen kunt ombuigen.
Maar dat is niet alles. We werpen ook een licht op de subtiele maar diepe valkuilen die op de loer liggen binnen traditionele organisaties. Van een traditioneel bedrijfsbeleid tot schadelijke HR-protocollen, prestatie doelen of boekhoudregels***: deze onzichtbare barrières kunnen zelfs de meest goedbedoelde Lean-initiatieven laten ontsporen. Door deze obstakels snel te onderkennen en aan te pakken, vermijd je de valkuilen waar veel organisaties in vastlopen.
* Compleet met interactieve sessies en praktische huiswerkopdrachten tussen de workshopsessies door.
** True Lean verwijst naar de holistische benadering die geworteld is in de principes van continue verbetering en respect voor mensen van Dr. W. Edwards Deming. Dit in tegenstelling tot de oppervlakkige, op tools gebaseerde implementaties die in veel organisaties gangbaar zijn. True Lean legt de nadruk op een culturele transformatie en lange termijn success.
*** Sommige algemeen aanvaarde methoden, zoals Cost Accounting, zijn NIET GAAP-conform, maar worden toch gebruikt.
"Medewerkers zijn niet uw probleem, zij vormen uw oplossing."
Wil je meer weten over hoe je zowel de medewerkers alsook de leidinggevenden meer plezier geeft in het werk en je daarbij de kwaliteit verhoogt en de kosten en doorlooptijden reduceert? Neem vrijblijvend contact op. Je vindt het contactformulier hier, of op de contact pagina in het menu.
Essentrium, Rembrandtlaan 27, 6881CP Velp Nederland KvK Nr.: 59376023 BTW Nr. NL001190095B55